The story behind the story begins with a little digging (click link above). Looking through the wall details on this project I found XPS (extruded polystyrene), a thermoplastic material, detailed behind metal wall panels. I reached out to the architect and setup a meeting.
To pass a NFPA 285 assembly fire test, XPS has several obstacles when designed in the exterior cavity as the "ci" component. All window and door header details require special, non-standard detailing, involving 4 pcf mineral safing and steel angles to protect the exterior cavity from excessive heat and flame entrance. Visit one of the XPS manufacturer's websites and you should find rough opening details reflecting these requirements. As a thermoplastic material, XPS is pliable when exposed to heat above 160 degrees F and will start to melt just over 200 degrees F. Given exposure to a flame, XPS rigid foam will quickly melt and drip.
Examining NFPA 285 assemblies after they've been through the 30 minute burn test, the results show melted XPS material most prominently at the header but also near the jambs and under the sill when special rough opening detailing is not in place. The thermoplastic XPS has the ability to burn up the wall assembly as well as spread fire down the wall too. When it comes to metal exterior skins, a popular cladding for almost all building types these days, XPS behind the metal wall panels will not pass an NFPA 285 test without sandwiching the insulation between two pieces of gypsum board. Not a practical way to design a wall assembly. In comparison, polyiso has gained in popularity because of its thermal properties (6.0-6.5 R-Value per inch), ease of installation, and its ability to resist fire and heat.
A thermoset plastic, polyisocyanurate will only char and flake when exposed to a flame source, and will not soften in high heat situations. The physical property differences with polyiso compared to XPS material reflect well for polyiso, especially in NFPA 285 assembly test results. Although considered a combustible, polyiso does not require any special header detailing at rough openings and will pass NFPA 285 tests behind panels used as the exterior skin - without additional gypsum board. Regarding rough openings, the NFPA 285 testing Hunter XCI has had conducted by third-party laboratories has shown that the window framing alone is enough detailing to pass the assembly test. This is a huge testament to polyiso's fire retardancy.
Hunter XCI's CG (coated glass facer) polyiso board, highlighted in the article offers exceptional durability, vapor permeance, and a mile long list of NFPA 285 compliant assemblies which include, of course, assemblies utilizing exterior metal panels. With a similar price point to XPS, a higher R-Value per inch, and no special header detailing, Hunter XCI CG is an easy choice for exterior continuous insulation. The article is case-in-point.
- Darren
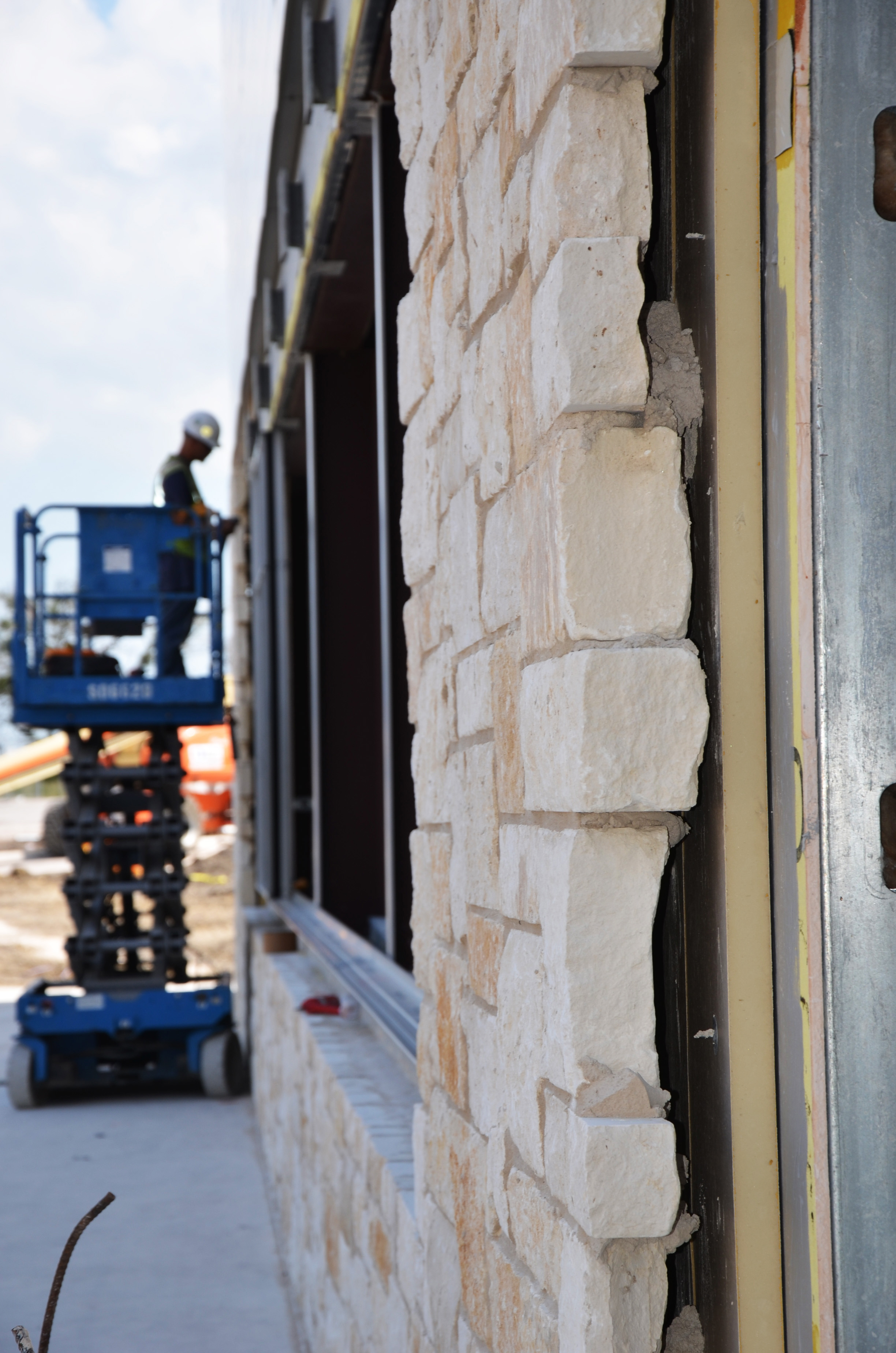

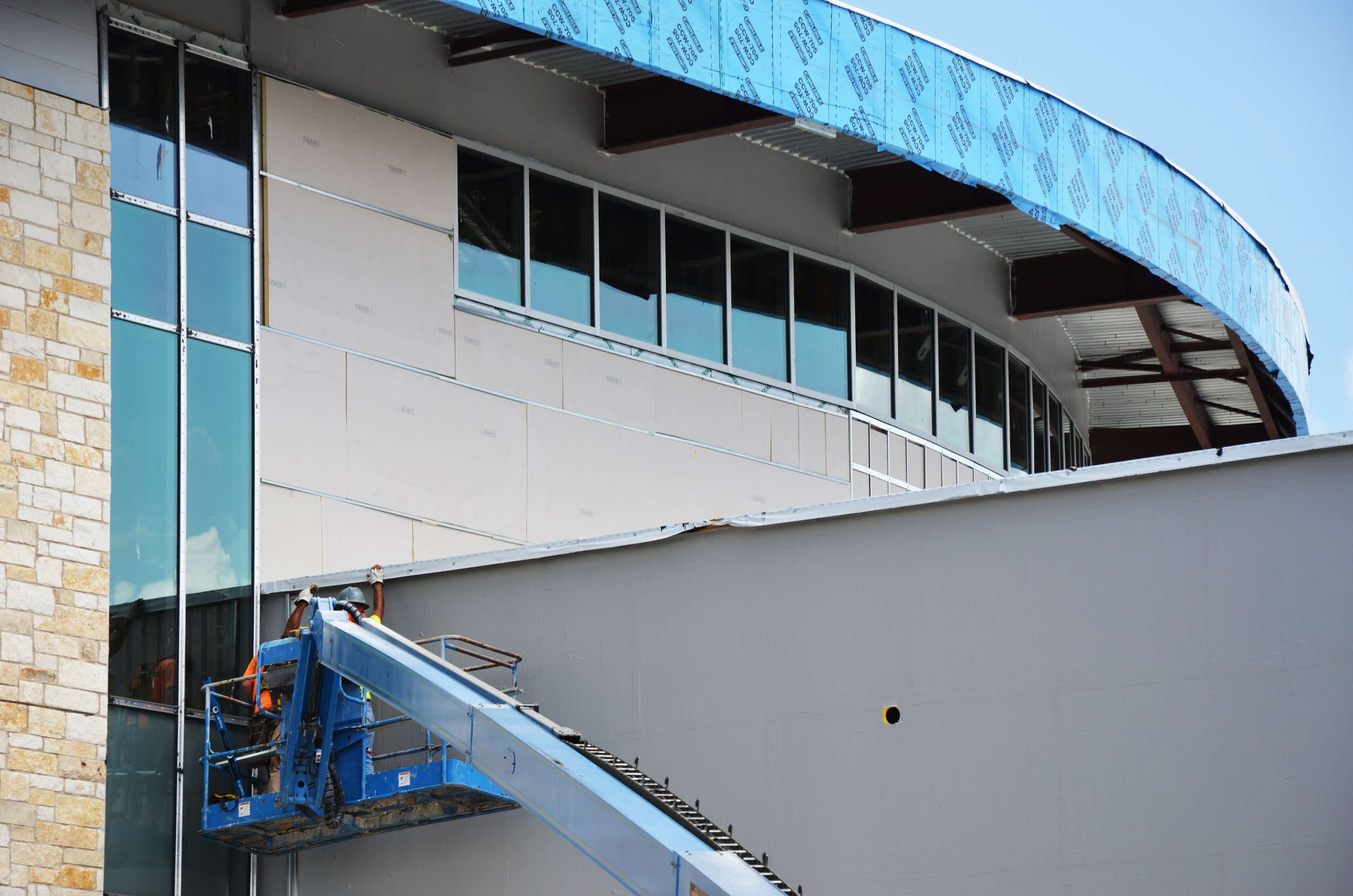
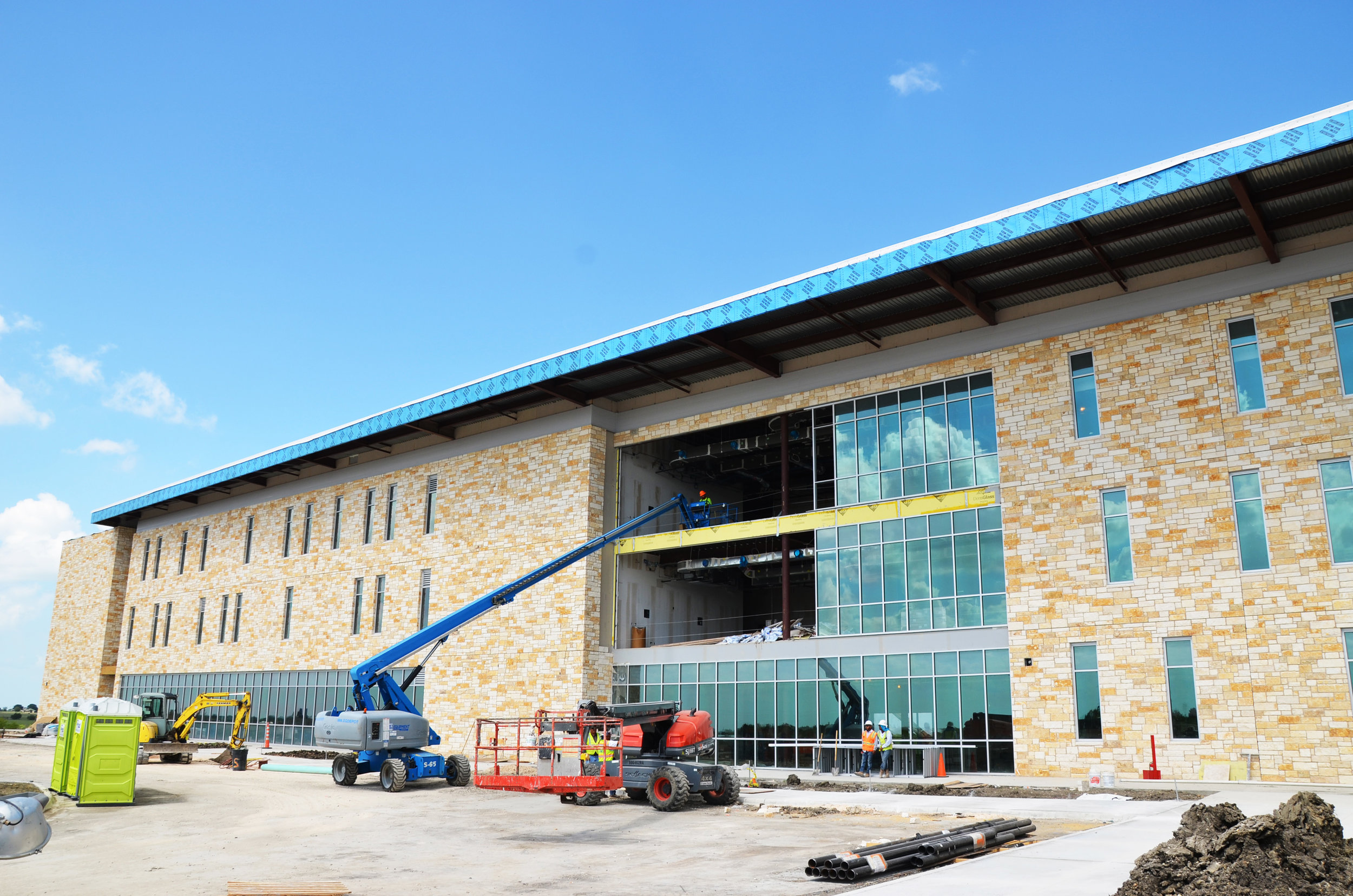
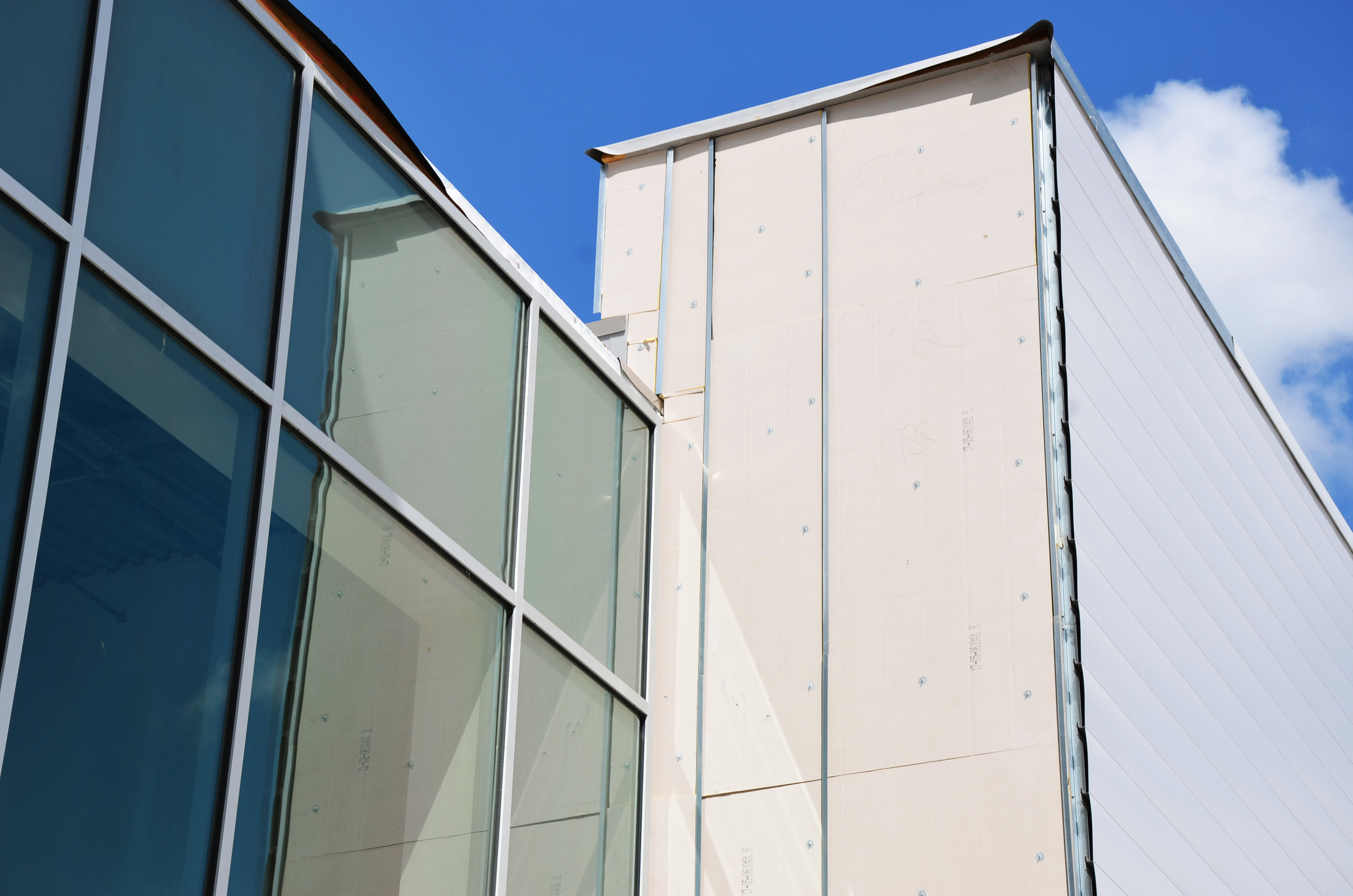
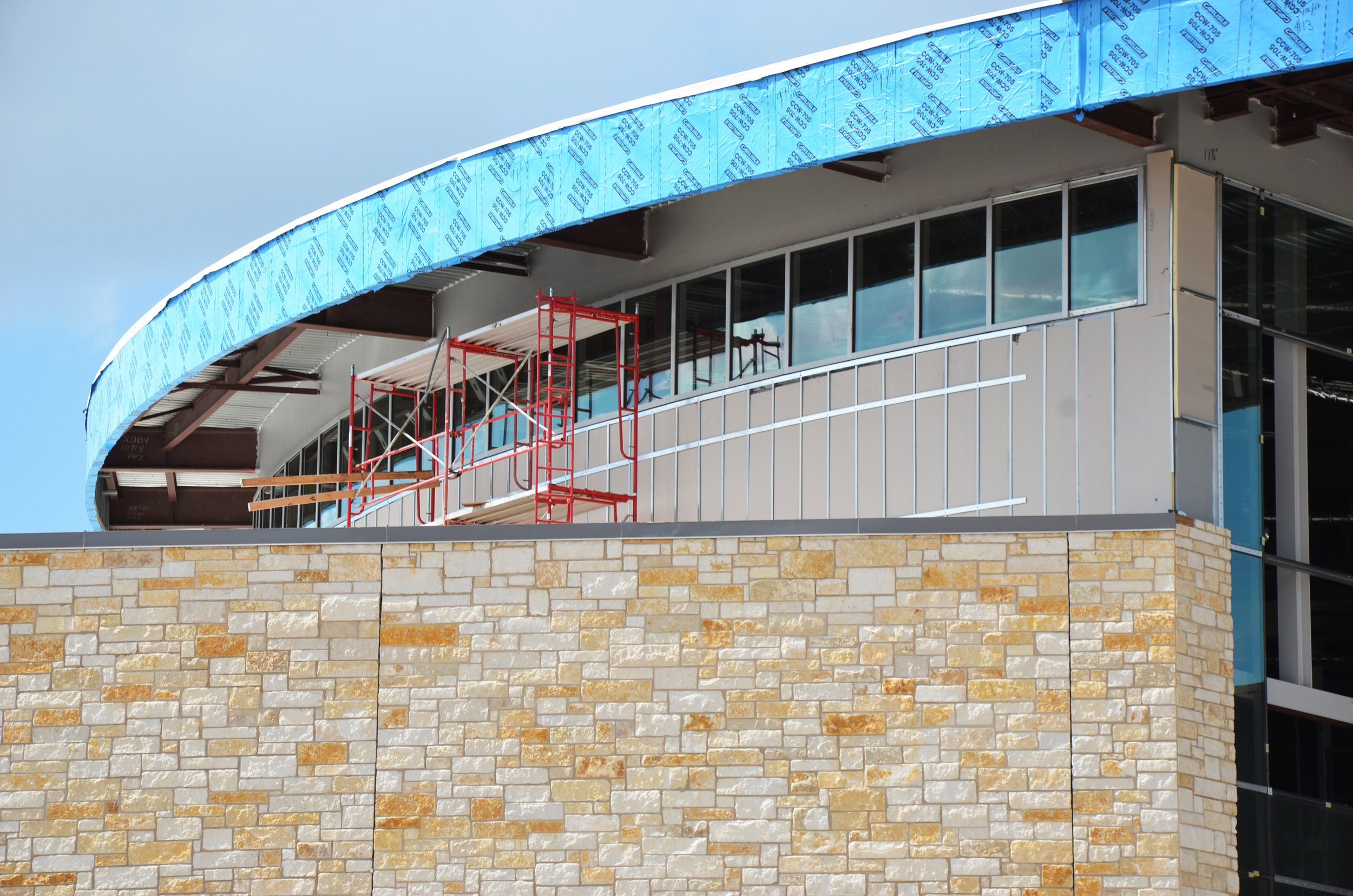
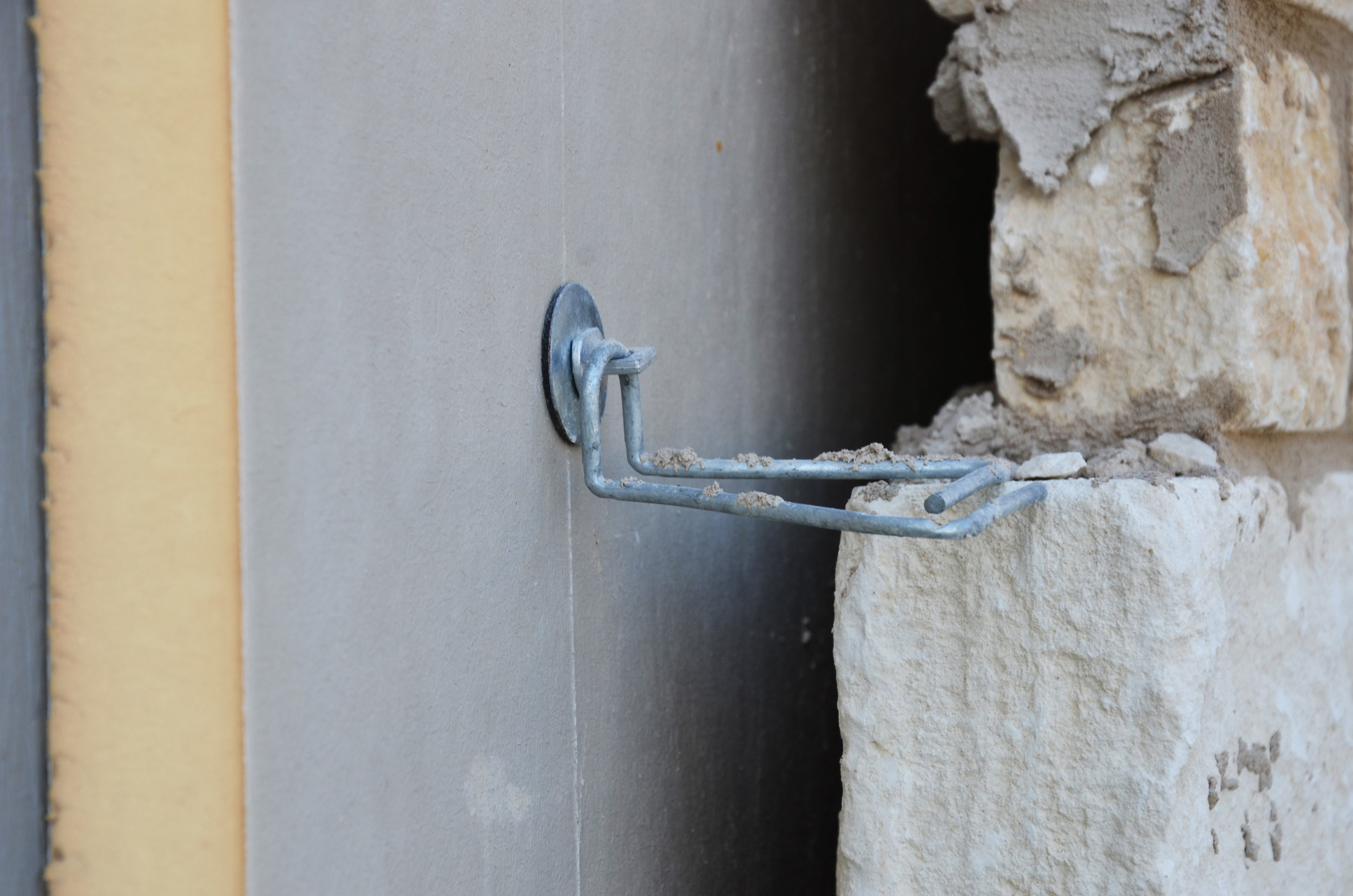
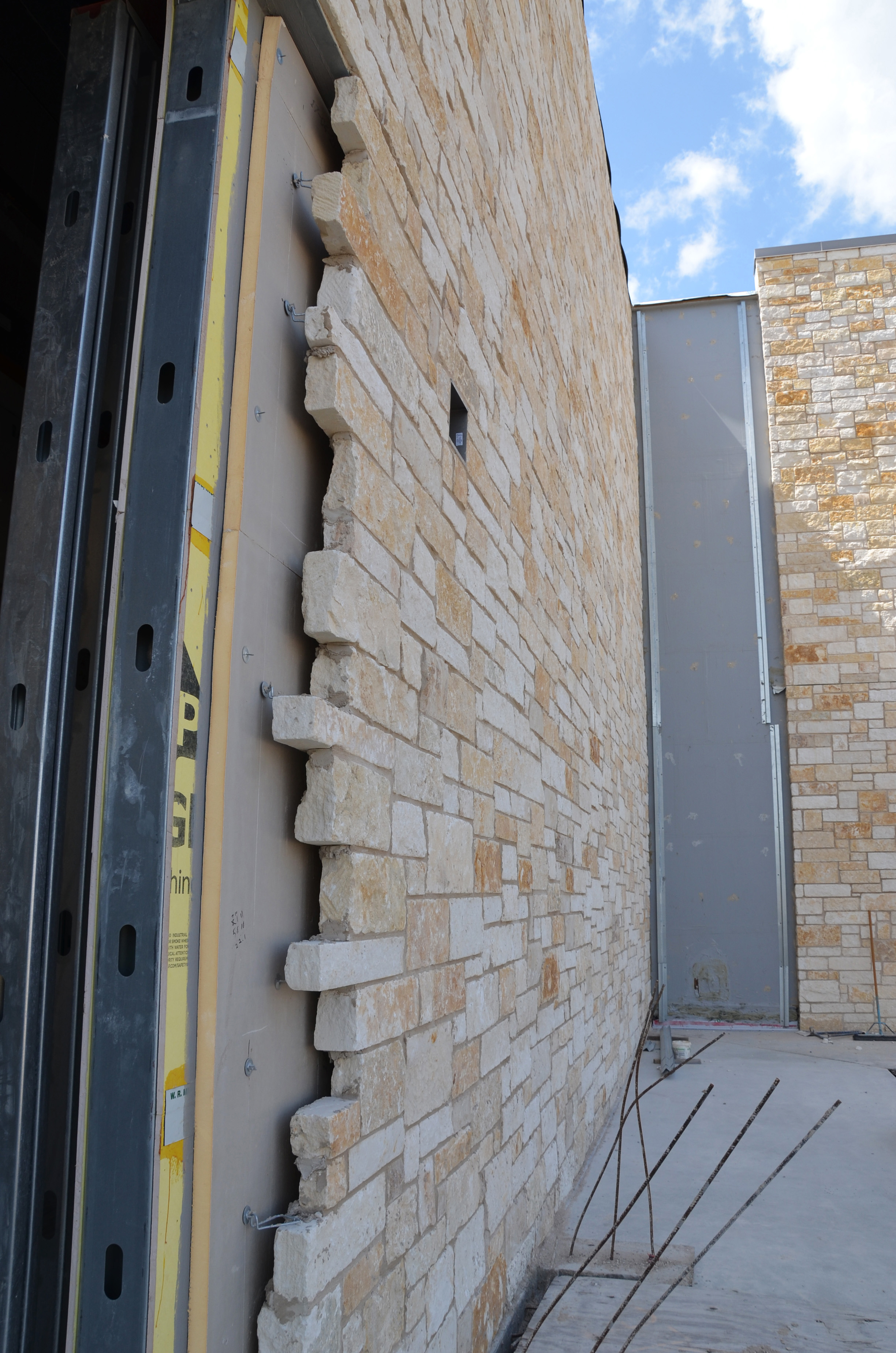